- Communicating Your Product Designs For Beginners
- Communicating Your Product Designs Online
- Communicating Your Product Designs Using
- Figure out what key things you want to communicate to your consumer when they first lay eyes on your business’ product, website, brand etc. And create a design that works to reflect this. It sounds like a hefty task, but it’s most definitely possible with a little planning and a lot of faith in the design process.
- Communicating product design Much of your time as a product manager is spent designing product interactions with your design team and then communicating that product design to your engineering team. When working with your design team, speed of iteration is most important.
- Communicating Your Product Designs Shetara Edden. Marketing Manager at Maker’s Row, whose mission is to make the manufacturing process simple to understand and easy to access. Whether you are an established designer or aspiring fashion entrepreneur, properly communicating your design ideas is crucial to the outcome of your product.
Storyboarding for Product Design: Most people are familiar with the term 'storyboard' in relation to movies, as a way that film creatives communicate to set up shots and plan out the plot. But storyboarding is also a critical part of the design process. Just as the film industry use.
Mastering Effective Communication as a Product Manager
Communicating Your Product Designs For Beginners
Product managers spend much of their time communicating ideas, plans, designs, and tasks to their teams. This includes everything from emails communicating decisions, to presentations communicating product roadmaps, to specs communicating product designs, to bug tickets communicating errors in the product.
Mastering effective communication is known to be an accelerant to the dissemination of ideas, to team cohesion, and to even the motivation and inspiration of team members. Given this, it’s worth spending time as a product manager thinking about how you can improve the various communications you have with your team.
I wanted to share some of the best practices I’ve observed on effective communication around the three high level responsibilities of product managers: vision, design, and execution.
Communicating the vision
A compelling product vision communicates the audience you are targeting, the distinct problem you are solving, and the unique solution by which you’ll win the market.
It’s important to come up with a succinct version of your vision that is no more than a quick elevator pitch. In doing so, you’re forced to carefully consider each word you include to understand if it’s really tantamount to what you’re trying to accomplish. This vision statement can then be used anytime you are asked to describe the product. I tend to include it at the beginning of most of my written specifications as well as in most of my product decks as a brief introduction and reminder to everyone what exactly it is that we are trying to achieve. While it may seem repetitive to do so, it’s extremely important to be consistent and constantly remind all stakeholders of it to ensure everyone stays on the same page.
Beyond the elevator pitch, I find it helpful to also prepare a more detailed presentation that answers the three vision questions of target audience, problem, and solution in greater detail. When I first engage with new team members or partner teams, I walk them through this presentation so they can quickly understand what we’re trying to accomplish. I also refine and review this at least quarterly with my own team. This helps ensure that the entire team is constantly making day-to-day decisions with our overall vision in mind.
Communicating product design
Much of your time as a product manager is spent designing product interactions with your design team and then communicating that product design to your engineering team.
When working with your design team, speed of iteration is most important. I usually start at the wireframe level to explore various information architectures and interaction flows. I then move quickly to high fidelity mockups with real user data (as opposed to lorem ipsum filler text). With high fidelity mockups you can really communicate the actual product experience which is important when designing interactions. However, given the skills of your design team, sometimes staying at the wireframe level longer enables faster iteration, which could be a valuable trade-off.
When communicating finalized product designs to your engineering team, it’s important at that point to definitely have high fidelity mockups with real user data as well as design specs that provide details on the UI as well as interaction behavior.
The level of specificity you communicate within your design specs really depends on the engineering team you are working with. I’ve worked in organizations like Microsoft where it was typical to author 30 page specifications detailing all of the interactions and error cases for the developer to implement. I’ve also worked at startups where the design specs were nothing more than the high fidelity mockups with no details beyond that. I tend to prefer a level of specificity that’s somewhat in the middle, with a bias towards lighter weight specifications. The best model I’ve seen for this is the Eric Ries model of converting the spec writing process from push to pull. The idea here is to start with a lightweight design spec, present it to the engineering team, and see what questions they ask. Then quickly iterate with them and document the discussions that come out of the process.
Communicating day-to-day execution
The vast majority of your time as a product manager is spent in day-to-day execution. This is where I’ve found it most helpful to have a formal process to ensure no small task or bug gets forgotten and to ensure effective communication of the highest priority tasks to the team.
The best way to do this is simply to use a task management tool and enforce a process around it. My personal favorite tool is Asana, as I find it an extremely lightweight way to create, assign tasks, and add additional details as necessary. We currently use JIRA at LinkedIn, which is more appropriate for larger teams where the custom filters and dashboards become more helpful. Regardless of what tool you use, the most important part is ensuring the rest of the team understands that’s where they go to find out what they need to work on, to report bugs, and to understand the team’s progress.
Beyond this, I find it's sometimes helpful to also send out weekly or monthly status emails to provide a summary of progress and more importantly to communicate how that progress fits into the larger picture of overall execution against the roadmap.
These tips should arm you with ways that you can improve your communication across the core responsibilities of vision, design, and execution.
FREE K-12 standards-aligned STEM

curriculum for educators everywhere!
Find more at TeachEngineering.org.
Quick Look
Grade Level: 10 (9-12)
Time Required: 45 minutes
Lesson Dependency: None
Subject Areas: Science and Technology
Summary
Students are introduced to detail drawings and the importance of clearly documenting and communicating their designs. They are introduced to the American National Standards Institute (ANSI) Y14.5 standard, which controls how engineers communicate and archive design information. They are introduced to standard paper sizes and drawing view conventions, which are major components of the Y14.5 standard. They can then practice their drawing skills by completing the associated activity to meet engineering standards.Engineering Connection
A revolutionary idea has value only if it can be effectively communicated. For engineers to imagine, create and design the products, devices and systems that have lasting impact on society, they must know how to present and archive their designs in a manner that is understood by all engineers across cultural and geographical boundaries. Given proper detail drawings, manufacturers know exactly how parts are created without the need for additional verbal explanation from engineers. A detail drawing stands on its own, so to speak, and provides a record or archive of the engineer's precise intent. Well-crafted detail drawings preserve creative work from one generation to the next.
Learning Objectives
After this lesson, students should be able to:
- Identify seven views of a detail drawing.
- List the important components of a detail drawing.
- List the paper sizes used for a detail drawing.
- Explain the role of standards in the preservation of technology.
Educational Standards Each TeachEngineering lesson or activity is correlated to one or more K-12 science, technology, engineering or math (STEM) educational standards.
All 100,000+ K-12 STEM standards covered in TeachEngineering are collected, maintained and packaged by the Achievement Standards Network (ASN), a project of D2L (www.achievementstandards.org).
In the ASN, standards are hierarchically structured: first by source; e.g., by state; within source by type; e.g., science or mathematics; within type by subtype, then by grade, etc.
Each TeachEngineering lesson or activity is correlated to one or more K-12 science, technology, engineering or math (STEM) educational standards.
All 100,000+ K-12 STEM standards covered in TeachEngineering are collected, maintained and packaged by the Achievement Standards Network (ASN), a project of D2L (www.achievementstandards.org).
In the ASN, standards are hierarchically structured: first by source; e.g., by state; within source by type; e.g., science or mathematics; within type by subtype, then by grade, etc.
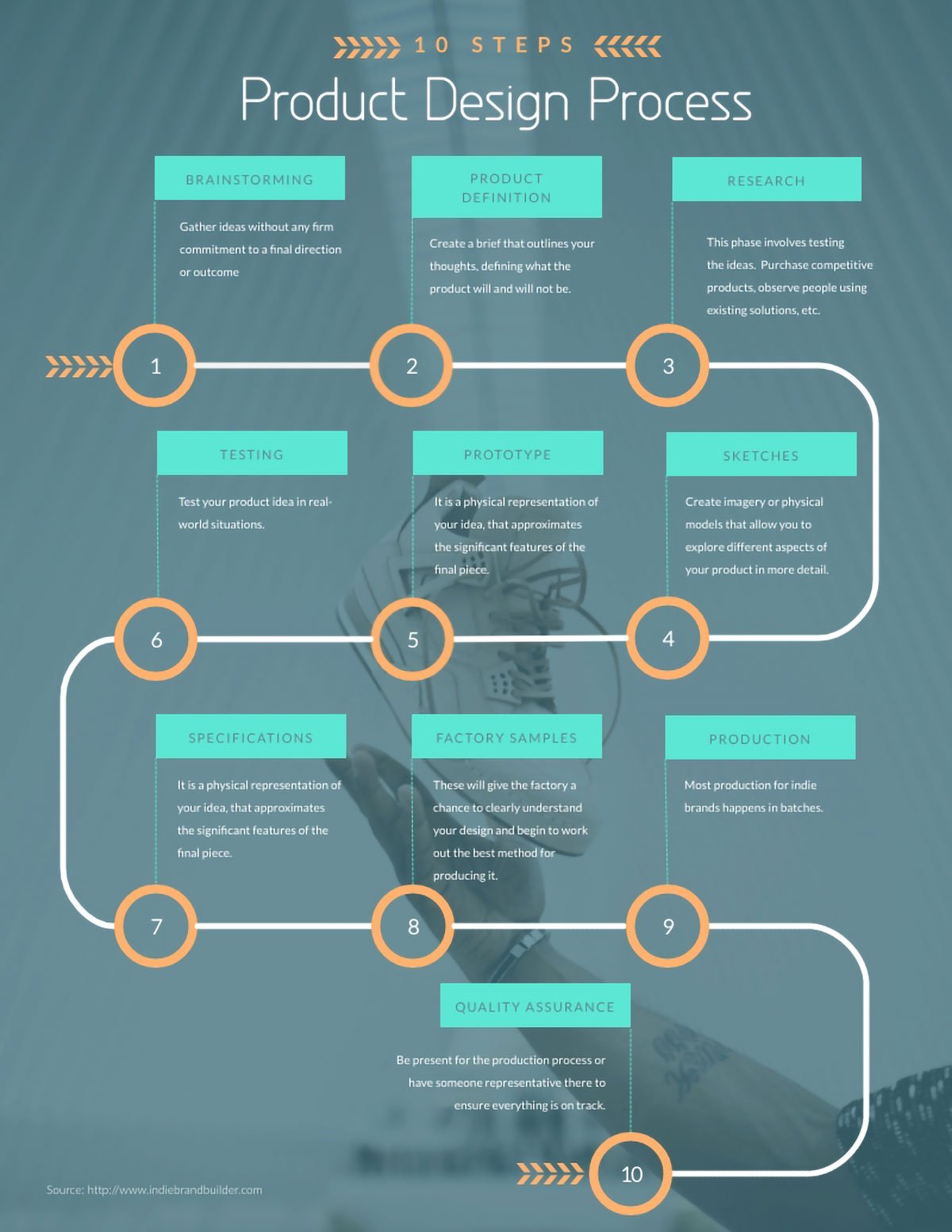
International Technology and Engineering Educators Association - Technology
- Expressing ideas to others verbally and through sketches and models is an important part of the design process. (Grades K - 2) More Details
Do you agree with this alignment? Thanks for your feedback!
- There are many ways to communicate information, such as graphic and electronic means. (Grades 9 - 12) More Details
Do you agree with this alignment? Thanks for your feedback!
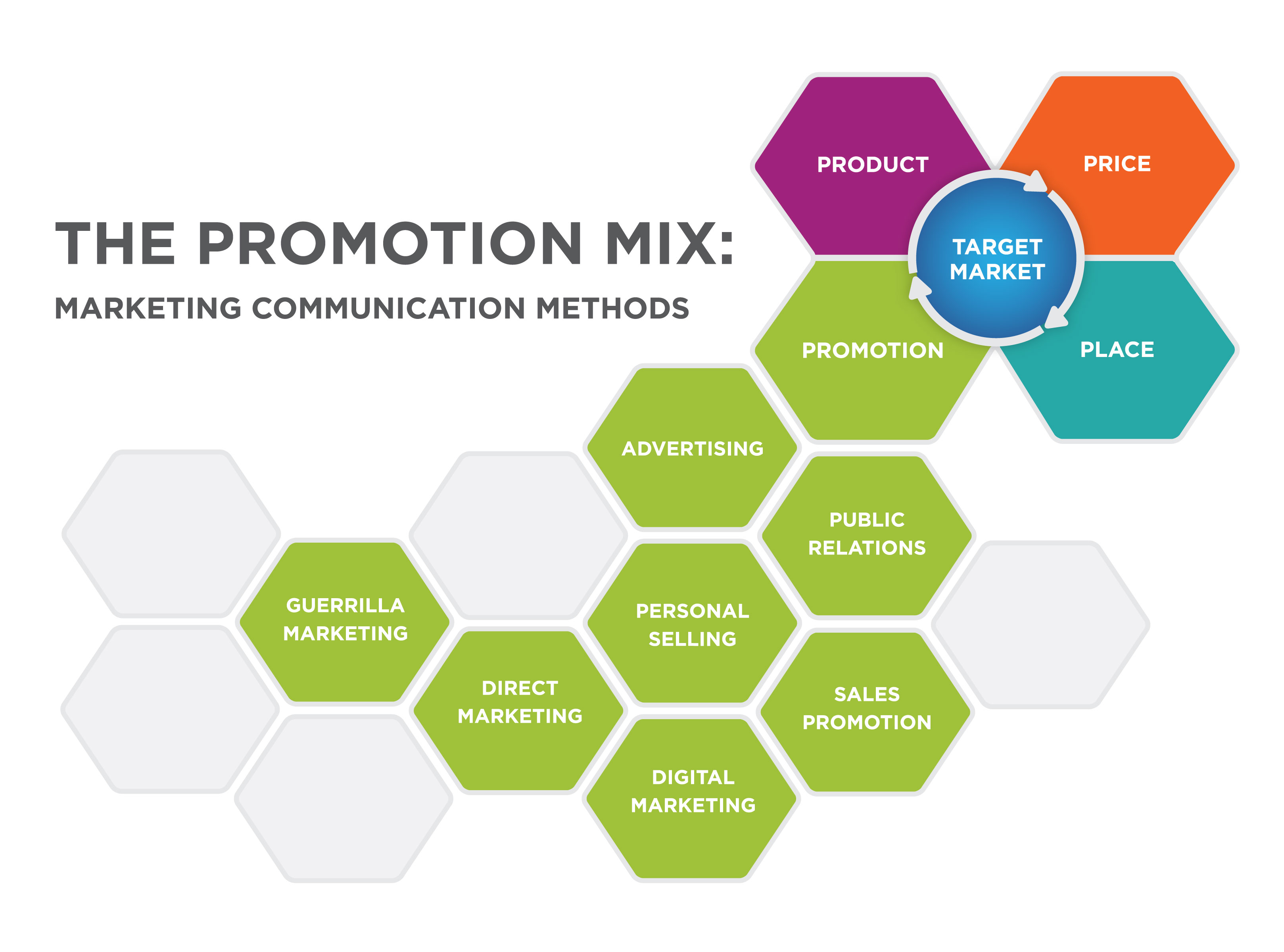
Worksheets and Attachments
Visit [www.teachengineering.org/lessons/view/cub_detdrawings_lesson01] to print or download.Introduction/Motivation
Communicating Your Product Designs Online
Engineers do not manufacture their own creative work, but typically communicate their ideas to highly trained machinists and manufacturers, who then construct the various components that make up the designs. Engineers also must present their designs in a way that is understood by engineers in different countries and cultures. Engineers also leave a legacy of creative thought through their designs. To preserve this technology from one generation to the next, it must be well-documented. How would you do this? How do engineers do this? A detail drawing is a tool used by engineers to communicate their designs to manufacturers and to preserve their work for future generations.
To facilitate the sharing of design information, engineers have created uniform standards, protocols and tools. One of these standards is called the ANSI Y14.5, which is a description for how to create a 'detail drawing.' A detail drawing is a two-dimensional representation of an engineer's design that contains all the information needed to precisely reproduce it. Detail drawings are especially useful when an engineer wants to manufacture their design. Given a proper detail drawing, a manufacturer knows exactly how to create a part without the need for additional verbal explanation from the engineer. The detail drawing stands on its own, so to speak, and provides a record or archive of the engineer's precise intent.
(Show students example detail drawings and describe information from the Lesson Background section. Use the Detail Drawing Visual Aids, which provides Figures 1-3, in a format suitable for overhead projection or handouts. Then administer the attached quiz and conduct the associated activity.)
Lesson Background and Concepts for Teachers
A 'detail drawing' is a drawing of a single component, assembly of multiple parts, or an entire system of assemblies. A detail drawing provides complete and precise descriptions of a part's dimensions, shape and how it is manufactured. A detail drawing should be concise, in that it conveys only the information needed to create the part. Information such as the exact size, type of material, finish, tolerance and any special shop instructions that are necessary to create the part are included its detail drawing.
Detail drawings are created on standard paper sizes. The 'North American Standard Paper Size' is specified by the ANSI Y14.5 standard and is used in the US. Figure 1 shows the different North American Standard paper sizes. The smallest size is designated by the letter 'A' and is the size of a typical sheet of notebook paper (8 ½ x 11 inch). The largest size is 'E,' which is equivalent to 16 sheets of notebook paper.
An engineer 'scales' very large or small objects in their drawings. For example, the components that make up a 1-inch microrobot are too small to draw to scale due to feature sizes that are not easily seen unmagnified. An appropriate scale, say 1/10 inch = 1 inch, is chosen to convey the necessary details, and then an appropriate paper size is chosen. The scale of the drawing is noted in the title block.
The following information should be present on a detail drawing:
- engineer's name
- part name
- material type
- drawing scale
- date and/or revision
- necessary views (front, left side, right side, top, bottom, and/or back)
- isometric view
- all necessary dimensions (width, depth, height, size, etc.)
- all dimension tolerances
Figure 2 is an example of a detail drawing that contains all the necessary information to create this component. Note the following from this drawing:
- the engineer's name (Ben Terry)
- part name (Tube, Base .3125 OD X .242 ID)
- part name (Tube, Base .3125 OD X .242 ID)
- scale (5:1)
- revision (B-01)
- the paper size: (A)
- the isometric view (upper right corner)
- the front view (upper left corner)
- bottom view (lower left corner)
- right view—in this case a section view (SECTION A-A)
- dimensions and allowable tolerances
In a detail drawing, views are included to clearly describe a three-dimensional object through the medium of two-dimensional paper. The front view is the first view that is chosen and is the only view that is arbitrary, that is, the engineer defines (decides) which view will be the front view. All other views are based off of the chosen front view. Views are positioned on the paper according to the convention illustrated by Figure 3.
Note that the views are obtained by rotating the front view. For example, the front view is rotated 90° to the left to obtain the left view, the front view is rotated 90° to the right to obtain the right view, the right view is rotated 90° to the right to obtain the back view, and so on. Note that the isometric view is obtained by considering the component within a cubical room looking towards the opposite, lower corner from an upper corner. Views need not be labeled as they are in Figure 3; their locations in the detail drawing relative to the front view defines each view. Sketching the views by hands takes practice. The associated Drawing Designs in Detail activity provides an opportunity for students to practice drawing the standard views.
The convention used in Figure 3 is called 'third angle projection,' which is used by North American manufacturers. Another convention, called 'first angle projection,' is used in Europe and Asia.
Associated Activities
- Drawing Designs in Detail - Students practice creating rudimentary detail drawings. They learn how engineers communicate the technical information about their designs using the basic components of detail drawings. They also practice creating their own drawings of a 3D block.
Vocabulary/Definitions
ANSI: Acronym for American National Standards Institute.
drawing view: A two-dimensional line drawing of an object as seen from a particular angle. The seven standard views are: front, back, top, bottom, left side, right side, and isometric.
scale: The scale of a drawing is defined as the ratio of a distance on the drawing to the corresponding distance on the actual object.
third angle projection: The convention for drawing views used in North America. A simple way to visualize third angle projection is to place the object in the bottom of an imaginary bowl. Sliding the object up the right edge of the bowl reveals the right side view, sliding up the left edge of the bowl reveals the left side view, and so on.
tolerance: The acceptable deviation of the actual value from a specified value.
Assessment
Lesson Summary Assessment
Quiz: After the lesson, administer the attached Detail Drawings Quiz to students, which asks them to identify drawing view perspectives and explain why the rules and procedures for creating detail drawings are so comprehensive and thorough. Review their answers to gauge their comprehension of the subject matter.
Copyright
© 2010 by Regents of the University of Colorado.Contributors
Benjamin S. Terry; Stephanie Rivale; Denise W. CarlsonSupporting Program
Integrated Teaching and Learning Program, College of Engineering, University of Colorado BoulderAcknowledgements
The contents of this digital library curriculum were developed under a grant from the Fund for the Improvement of Postsecondary Education (FIPSE), U.S. Department of Education and National Science Foundation GK-12 grant no. 0338326. However, these contents do not necessarily represent the policies of the Department of Education or National Science Foundation, and you should not assume endorsement by the federal government.
Last modified: January 19, 2021
Communicating Your Product Designs Using
Find more at TeachEngineering.org